Revealing the Art of Light Weight Aluminum Spreading: A Comprehensive Guide for Beginners
In the realm of metalworking, aluminum spreading stands as a craft that marries artistry with precision. As newbies begin on this journey, they are faced with a labyrinth of techniques, devices, and security procedures that develop the structure of mastering the art of aluminum casting.
Background of Light Weight Aluminum Casting
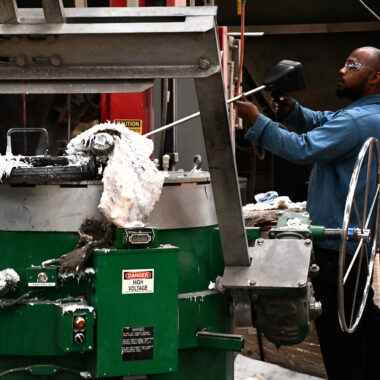
One of the crucial milestones in the background of aluminum casting was the innovation of the initial light weight aluminum casting equipment in 1886 by Charles Martin Hall. Over the years, improvements in modern technology have additionally refined the light weight aluminum spreading process, making it a lot more specific, economical, and eco pleasant.
Vital Tools for Beginners
When beginning on the trip of aluminum casting as a newbie, obtaining the important tools is extremely important for making sure a smooth and effective casting procedure. A crucible, generally made of graphite or clay-graphite, is basic for thawing light weight aluminum. Crucible tongs are required for handling the warm crucible safely. A heater, either electric or gas-powered, is crucial for thawing the aluminum to its liquid state. To eliminate contaminations and strengthened particles, a skimming tool is indispensable. A mixing pole assists in ensuring and mixing the molten light weight aluminum uniformity. Flask and molding sand are important for creating mold and mildews right into which the liquified aluminum is poured. A mold structure, containing drag and deal, is needed for molding the sand. Venting poles assist in creating channels for air and gas to leave from the mold and mildew during spreading. Finally, safety equipment such as heat-resistant handwear covers, apron, and face guard are essential for protecting oneself during the casting procedure. With these necessary devices in hand, beginners can start their light weight aluminum casting journey with confidence.
Standard Steps in Light Weight Aluminum Spreading
To launch the aluminum casting process effectively, newbies should first prepare the mold and guarantee its appropriate alignment within the mold and mildew structure. As soon as the mold and mildew prepares, the next step includes thawing the light weight aluminum. This can be done using a furnace or a basic gas lantern, depending on the scale of the project. The liquified light weight aluminum is then meticulously dig this poured into the mold, filling it to the brim. It is vital to allow the light weight aluminum adequate time to solidify and cool inside the mold and mildew prior to trying to remove the casting.
After the light weight aluminum has cooled down and solidified, the mold needs to be opened to expose the newly formed casting. Grasping these fundamental actions is important for newbies looking to dig right into the art of light weight aluminum casting.
Common Sorts Of Aluminum Alloys
Among the essential considerations in aluminum casting is comprehending the diverse range of light weight aluminum alloys frequently used in the procedure. Light weight aluminum alloys are identified based upon their chemical composition and properties, with each kind offering special qualities fit for various casting applications. One typical aluminum alloy is A356, recognized for its superb castability and good mechanical homes, making it prominent in various industries such as auto and aerospace. One more commonly utilized alloy is 6061, valued for its high toughness and corrosion resistance, making it ideal for structural components and marine applications. Furthermore, the 380 alloy is preferred for its remarkable fluidity and machinability, making it a leading option for complex spreadings needing elaborate information. Understanding the buildings and official site benefits of these usual light weight aluminum alloys is vital for beginner wheels to choose one of the most proper alloy for their details casting demands, ensuring top quality outcomes in their spreading projects - aluminum casting illinois.
Safety Preventative Measures in Spreading Light Weight Aluminum
Thinking about the vital function of light weight aluminum alloys in the casting process, focusing on safety precautions is critical to guarantee a secure and effective spreading setting. When collaborating with liquified aluminum, it is vital to put on appropriate personal safety tools (PPE) such as heat-resistant gloves, aprons, encounter guards, and security goggles to stop injuries and burns. In addition, make sure proper ventilation in the spreading area to reduce exposure to damaging fumes and gases launched during the melting process.
To avoid prospective fires, constantly have a fire extinguisher nearby and establish a clear discharge strategy in case of emergency situations. It is vital to carry out routine safety training sessions for all workers associated with the spreading operation to inform them on finest practices and emergency procedures. Appropriate handling of equipment, including crucibles, ladles, and molds, is vital to avoid mishaps and preserve a safe workplace.
Moreover, keeping a clean and well organized work space can help in reducing the risk of slips, trips, and drops. By adhering to these safety and security preventative measures, newbies can create view it now a protected structure for understanding the art of light weight aluminum spreading.
Final Thought
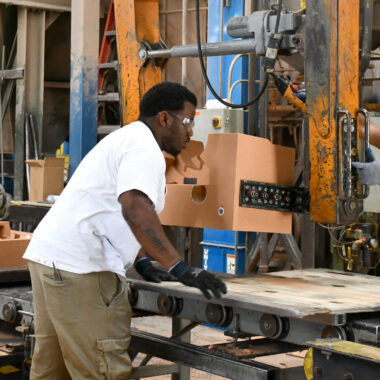
It was not up until the 19th century that significant advancements in aluminum spreading were made, particularly with the development of more efficient techniques for melting and shaping light weight aluminum alloys.
One of the key turning points in the background of aluminum spreading was the creation of the very first aluminum casting maker in 1886 by Charles Martin Hall.When beginning on the trip of light weight aluminum casting as a beginner, obtaining the necessary devices is vital for guaranteeing a smooth and successful spreading procedure.One of the vital considerations in aluminum casting is comprehending the varied variety of aluminum alloys typically utilized in the process. By understanding the standard steps and crucial devices entailed in light weight aluminum spreading, novices can successfully function with different kinds of light weight aluminum alloys.
Comments on “Specialists in Aluminum Casting Illinois: Elevate Your Manufacturing”